Navigating Capital Expenditure: A Handbook for Emerging Businesses
Ready to talk shop about early-stage manufacturing, eh? It ain't a walk in the park, but this guide is your GPS. Let's dive in!
Starting a manufacturing business is a tango of risk and rewards. You need physical assets, which require a chunk of change before you can even think of making a dime. That's a tough nut for any company to crack, especially an early-stage one. The secret? Smart money moves. Here's the play-by-play.
First off, there are two critical aspects of capital spending: what you can afford to spend, and what you should spend. The former depends on financing—how much cash you haul in from investors and how you use it. The latter is all about creating a competitive product in the marketplace.
How much you can spend is the cash limit. It comes down to how much investors are willing to fork over. So, what's the median deal size for various manufacturing sectors in 2023? Let's take a gander:
- Seed stage: $1-5M
- Series A: $3-7M (Utilities, Food & Beverage, Household Goods, Agriculture) to $10M+ (Automotive, Chemicals, Industrial Machinery)
- Series B: $14-22M (no deals for Household Goods, Utilities at $40M, Iron and Steel at $877M, others in between)
Now, this means some sectors, like Utilities and Iron and Steel Mining, can swing bigger bucks for capex. But even the largest sector deals can't fully fund a new custom factory.
What about debt? Well, you can use venture debt or equipment financing to help, but those plug only small gaps. As you grow, you'll unlock more debt options, like project financing or bank loans. But that's usually out of reach for early-stage companies.
So, what can you do? Start by purchasing only the essential assets. Household Goods and Food & Beverage sectors have few exceptions. For other industries, there may be room to wiggle, especially in Iron and Steel Mining. If you think you're the exception, be crystal clear with investors about why you need it.
Heads up: You might be able to spend up to $5M on capex in the beginning, increasing in later rounds. But remember, the capex spending has to match production. If not, your capital expenditure depreciation will weigh too heavily on your production.
If you feel compelled to build your own factory, securing funding becomes top priority. This is especially the case if you're building a custom, first-of-its-kind facility. Some companies have even used public funding, grants, and loans to make it happen. But this is the exception, not the rule.
Now, how much should you spend? It starts with Cost of Goods Sold (COGS). You gotta sell competitively priced products for the market. To do that, your COGS needs to be in line with comparable products. The contribution to COGS from capital expenditures takes the form of capital depreciation. To find the industry standard depreciation for COGS, research competitors selling similar products and make a capex budget that ensures you don't exceed it.
In short, play it smart with your capital. That's the key to navigating early-stage manufacturing. Make informed spending decisions, squeeze out every bit of efficiency, and you'll find success in this tough game. Good luck!
Enrichment Data:- Early-stage manufacturing companies need to plan their capital expenditure carefully, considering both financing capabilities and industry benchmarks. Key takeaways include: - Allocate funds wisely, prioritizing core assets over non-essential frivolities. - Leverage operating cash flow for equipment financing when possible. - Strive for tax-efficient depreciation schedules, like MACRS in the U.S. - Implement lean manufacturing principles to maximize asset efficiency.
Sources:1. IndustryWeek. 'Capital Expenditures: How to Determine What to Spend on CapEx in the Early Stages' (2023). https://www.industryweek.com/operations-management/manufacturing/capital-expenditures-determine-spend-capex-early-stages
- Investopedia. 'How to Calculate and Minimize Operations Costs' (2019). https://www.investopedia.com/articles/personal-finance/092915/how-calculate-and-minimize-operations-costs.asp
- Accounting Tools. 'Non-Operating Expenses: What They Are and How to Calculate Them' (2021). https://www.accountingtools.com/articles/2021/08/24/non-operating-expenses-what-they-are-and-how-to-calculate-them
- CFO Magazine. 'Capital Expenditure and Depreciation: The Relationship Explained' (2018). https://www.cfomag.com/news/2018/07/20/capital-expenditure-and-depreciation-relationship-explained/
- Investopedia. 'Capital Budgeting: Principles and Techniques' (2021). https://www.investopedia.com/terms/c/capital_budgeting.asp
- In the realm of early-stage manufacturing, shrewd capital expenditure planning is essential, balancing financing capabilities with industry benchmarks.
- Allocate funds prudently, prioritizing essential assets over non-essential spending, and leverage operating cash flow for equipment financing when available.
- Implement lean manufacturing principles to maximize asset efficiency and aim for tax-efficient depreciation schedules, like MACRS in the U.S.
- When making capital expenditure decisions, research competitors selling similar products to establish an industry standard depreciation for Cost of Goods Sold (COGS).
- Whether looking to minimize personal-finance risks or seeking a lucrative business investment, understanding the stages of capital expenditure and its relationship with depreciation can lead to success in early-stage manufacturing, even in sectors like technology.
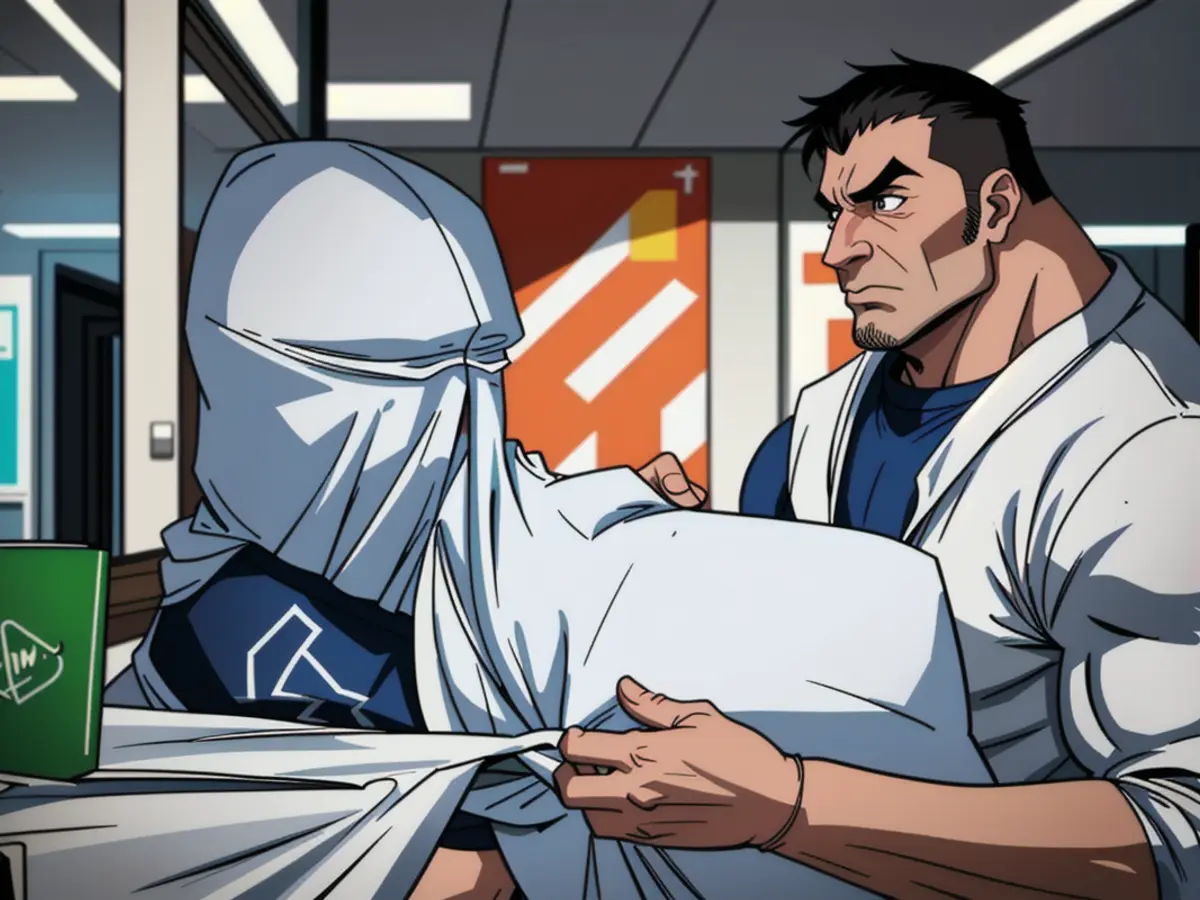
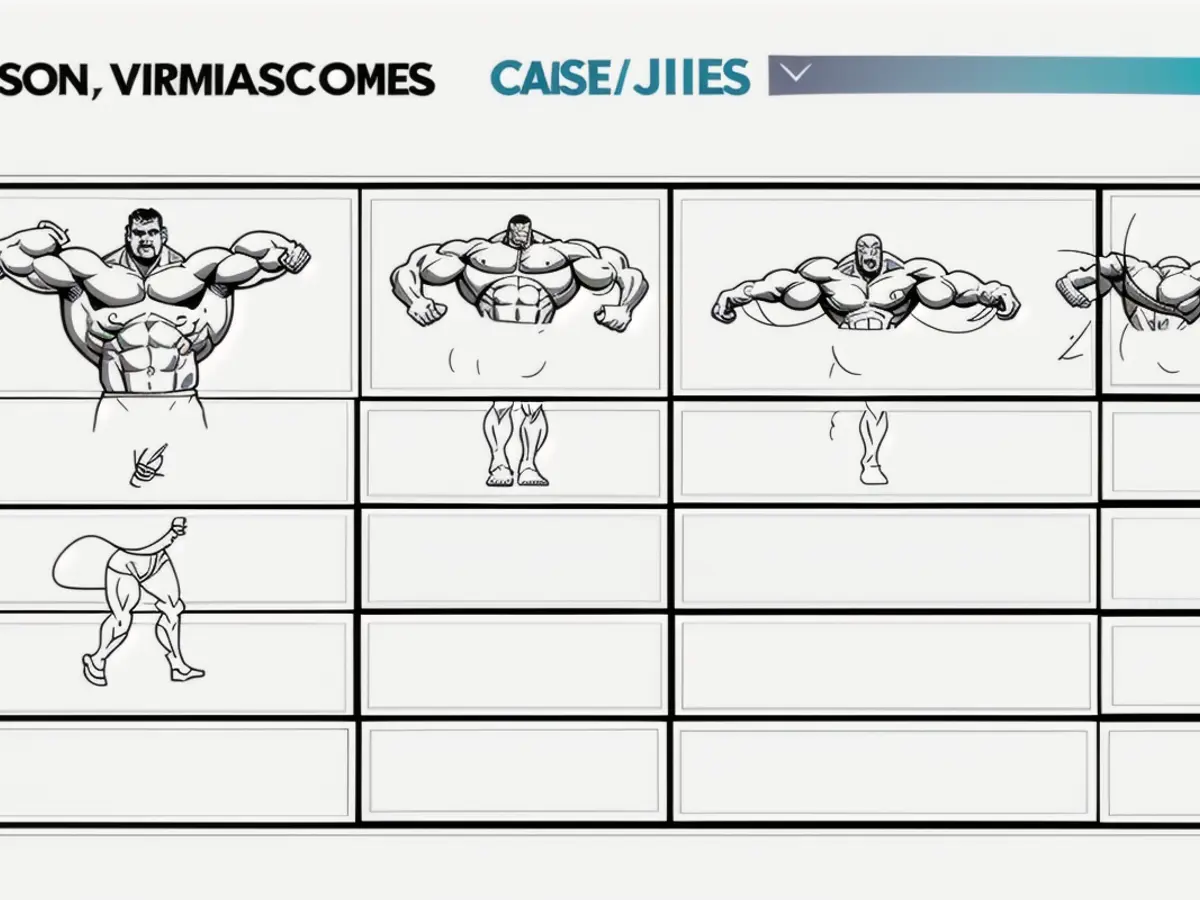
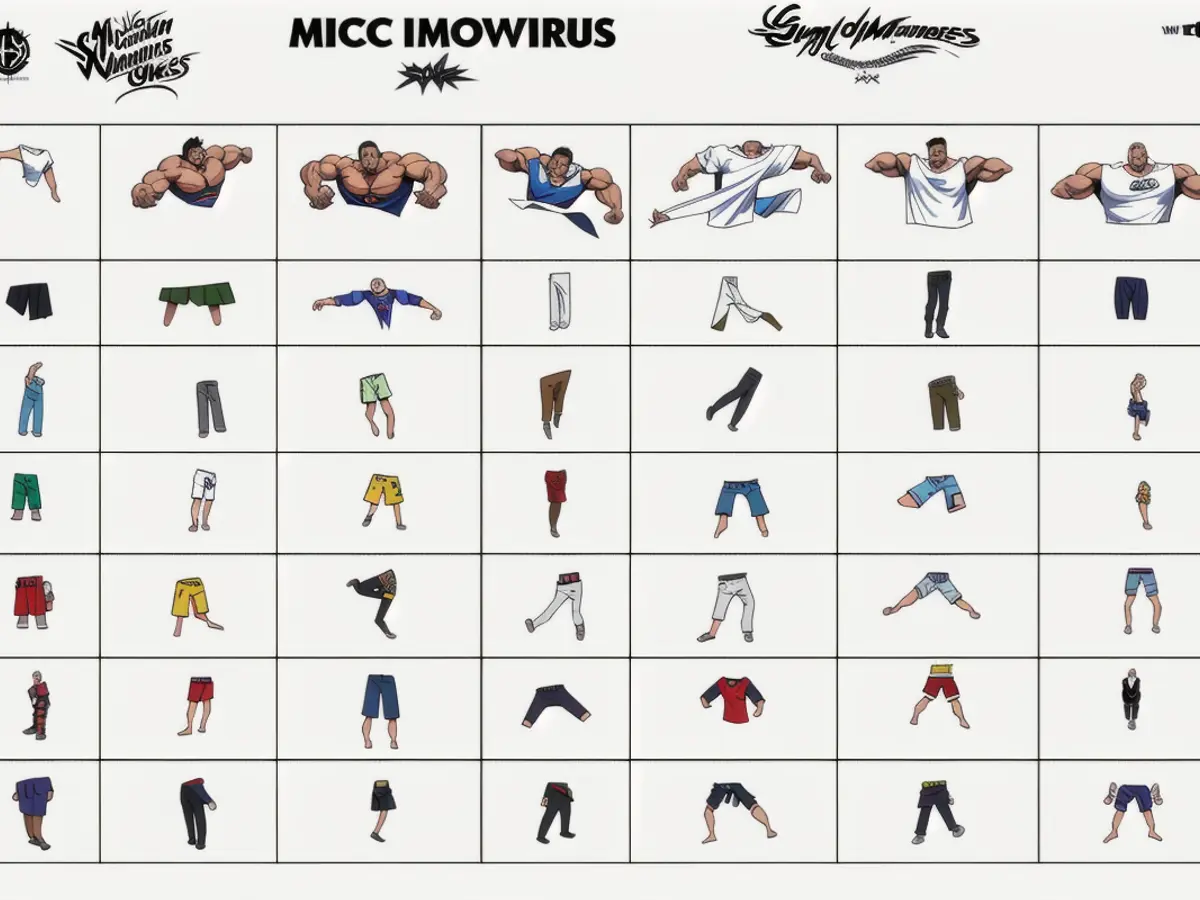