Vulnerabilities in Cybersecurity Remain Unaddressed, Threatening Manufacturers During Modernization Processes
A Warning Before Modernization: Securing Manufacturing's Digital Future
The industrial heartland of America is sprinting headlong into modernization without fully considering the pitfalls. The crux of the issue lies in the stark discrepancy between the old and the new. Industrial control systems (ICS) and SCADA networks were designed for solitude, never intended to link up with the internet. But today's digital revolution is forcing these systems online, creating a delicate balance between productivity and safety.
Take, for instance, a prominent global manufacturer. With the ambition to modernize its production facilities, they integrated their SCADA network with cloud-based analytics and remote monitoring solutions. However, in their haste, multiple SCADA endpoints were unintentionally left exposed to the public internet. Lacking strong authentication controls or segmentation, these supposedly secure systems became inviting targets for cybercriminals.
This situation turned out to be potentially disastrous, with unauthenticated access to SCADA systems potentially allowing attackers to manipulate industrial processes, leading to production delays. Given SCADA's control over physical machinery, any breach could expose workers to danger and jeopardize valuable assets. Moreover, the integrity of critical telemetry data was at stake, with unauthorized access posing the risk of altering parameters and resulting in faulty output.
To add to the industry's woes, numerous sectors enforce strict cybersecurity guidelines for ICS/SCADA, such as NIST 800-82 and IEC 62443. Ignoring these standards could result in hefty fines and irreversible damage to reputation.
This predicament serves as a siren call for an industry eagerly embracing the digital world, yet fails to fully grasp the associated risks. The manufacturing sector's infatuation with cloud computing and remote monitoring could undoubtedly boost efficiency, but it's also exposing vulnerabilities in systems unwittingly designed to stay isolated.
A Hidden Dilemma Unveiled
Do you remember the days when factory security could be ensured by nothing more than a locked door and a security guard? Today, our haste to modernize has resulted in connecting these very same systems to the internet, often through poorly secured cloud solutions and remote access tools.
In the aforementioned case, attackers could have seized control of factory equipment, posing a threat to workers, halting production, or causing even more severe consequences. Shockingly, the organization remained oblivious to its exposure, as traditional security tools overlooked these vulnerabilities.
It appears we're encountering a blind spot that's becoming alarmingly common in manufacturing. With the line between operational technology (OT) and information technology (IT) increasingly blurred, we need to fundamentally reassess how we monitor and protect our industrial systems.
Eyes Wide Shut: The Hidden Dangers
In spite of implementing standard security measures like vulnerability scanners and network monitoring, organizations frequently overlook their actual exposure. A telling example involves multiple major manufacturers, whose internet-facing OT assets went undetected during routine external scans. These oversights extended to exposed programmable logic controllers (PLCs), human machine interfaces (HMIs), and even remote terminal units (RTUs) that controlled industrial processes directly. These systems were outside the internal security teams' radar.
This phenomenon can be traced back to how industrial networks evolve. Savvy vendors could install cellular modems for remote maintenance, or diligent engineers may set up temporary VPNs for remote monitoring that eventually become permanent. Traditional security tools often fail to spot these exposures because they rely on outdated assumptions, such as scanning only known networks, checking only registered assets, and monitoring only documented systems. In today's manufacturing environments, characterized by shadow OT (unmanaged connections), this inside-out approach can leave dangerous gaps.
Gaining an Adversary's Perspective
Manufacturers must reassess how they monitor and protect their industrial systems. Instead of relying exclusively on internal network scans and predefined asset lists, an "outside-in" approach is preferred. This approach examines a manufacturer's infrastructure from an attacker's viewpoint.
This outside-in approach has already demonstrated effectiveness in real-world scenarios. One large manufacturer successfully employed outside-in reconnaissance to survey its externally exposed systems using observation techniques hackers would use to discover the best entrances to their organization. This exercise identified multiple internet-facing industrial systems that traditional security tools had missed, including exposed SCADA endpoints controlling critical production processes, industrial protocol converters service remote access, and human machine interfaces (HMIs) with default credentials still active.
Action Plan
Scout the External Terrain First. Given that over 80% of breaches involve external actors, it's crucial to identify what is visible from the internet first. Search the web for any internet-facing industrial assets, such as controllers, HMIs, protocol converters, and remote access solutions.
Cast a Wide Discovery Net. Don't limit security assessments to known assets or networks. Scan across all business units, subsidiaries, and acquisitions to discover "shadow OT"-industrial systems connected to the internet without security team awareness.
Test Thoroughly. Conduct comprehensive security testing for all exposed assets, not just the critical ones. This should encompass checking for default credentials, unpatched vulnerabilities, and insecure configurations specific to industrial systems.
Consider Impact over Technical Severity. Prioritize the vulnerabilities to address based on their business implications, such as operational dependencies, safety impacts, and sector-specific regulatory requirements.
Spread the Knowledge. Ensure that discovered exposures are shared with all relevant stakeholders-from security teams to operations staff to executive leadership-to facilitate coordinated remediation efforts.
Learning the Hard Way
While the consequences of the aforementioned incident proved to be fortuitous, with vulnerabilities discovered and addressed before they could wreak havoc, the attack surface continues to expand. Modernization in manufacturing is an inevitable reality, but its success relies on prioritizing security. While the advantages of digital transformation are substantial, they can only be fully realized if we view cybersecurity not just as an IT concern, but as a core operational risk requiring leadership attention. The time for action is now; secure these newly connected systems before attackers exploit them, and we learn these lessons the hard way.
Securing the Industrial Landscape
With the proper preparation, manufacturers can reap the benefits of digital transformation without inviting dire risks. To achieve this balance, consider the following best practices:
- Asset Visibility and Inventory Management: Develop an all-embracing, automated asset inventory to identify and track every connected device, including legacy OT systems and IoT endpoints. Tools such as Claroty’s CPS security solutions provide granular asset tracking to detect unauthorized devices and maintain real-time network mapping[1][2].
- Network Segmentation and Perimeter Defense: Utilize firewalls and secure gateways (like data diodes) to isolate OT networks from IT/cloud systems, restricting lateral movement during breaches[4][5]. Prioritize crucial zones for network monitoring and threat detection at choke points between production cells and data centers to filter suspicious traffic[4]. Implement unidirectional data flows using secure gateways to prevent external intrusions in high-risk areas[4][5].
- Vulnerability and Exposure Management: Focus on actively exploited vulnerabilities and insecure configurations rather than generic scans. Combine automated patching with manual validation to avoid operational disruptions. CISA’s ICS advisories offer targeted guidance for addressing vulnerabilities in Schneider Electric and similar systems[3].
- Threat Detection and Response: Employ real-time anomaly detection by deploying IDS/IPS solutions fine-tuned to OT protocols to detect unusual command patterns or data flows[4][5]. Implement behavioral monitoring to track deviations from normal operations, such as unauthorized PLC reprogramming attempts or abnormal sensor readings[5].
- Access Control and Governance: Establish zero-trust policies, employ role-based access controls (RBAC), and insist on multi-factor authentication for remote maintenance sessions. Regularly reinforce technical controls (like secure gateways) with staff training to boost incident response accuracy[4][5].
- Security-Integrated Digital Transformation: Prioritize vendors providing embedded security features, such as encrypted machine communication and secure over-the-air (OTA) updates. Examples such as Shoplogix’s approach demonstrate how real-time data analytics can coexist with network segmentation and access controls without inhibiting operational efficiency[5]. Avoid overreliance on air-gapped assumptions as modern IIoT ecosystems inherently require secure external connectivity[5].
- In modernization efforts, many SCADA systems are connected to the internet through cloud solutions and remote access tools, creating risks for unauthenticating attackers to manipulate industrial processes or compromise telemetry data.
- The manufacturing industry must reevaluate its security approaches to account for the increasing exposure of operational technology (OT) assets in digital networks, with an emphasis on the "outside-in" perspective that considers the attacker's viewpoint.
- To secure industrial landscapes during digital transformation, manufacturers should prioritize asset visibility and inventory management, network segmentation, vulnerability and exposure management, threat detection and response, access control and governance, and security-integrated digital transformation.
- Ignoring industry cybersecurity standards, such as NIST 800-82 and IEC 62443, could result in hefty fines and irreversible damage to reputation, demonstrating the critical importance of fully understanding and addressing the risks associated with modernization.
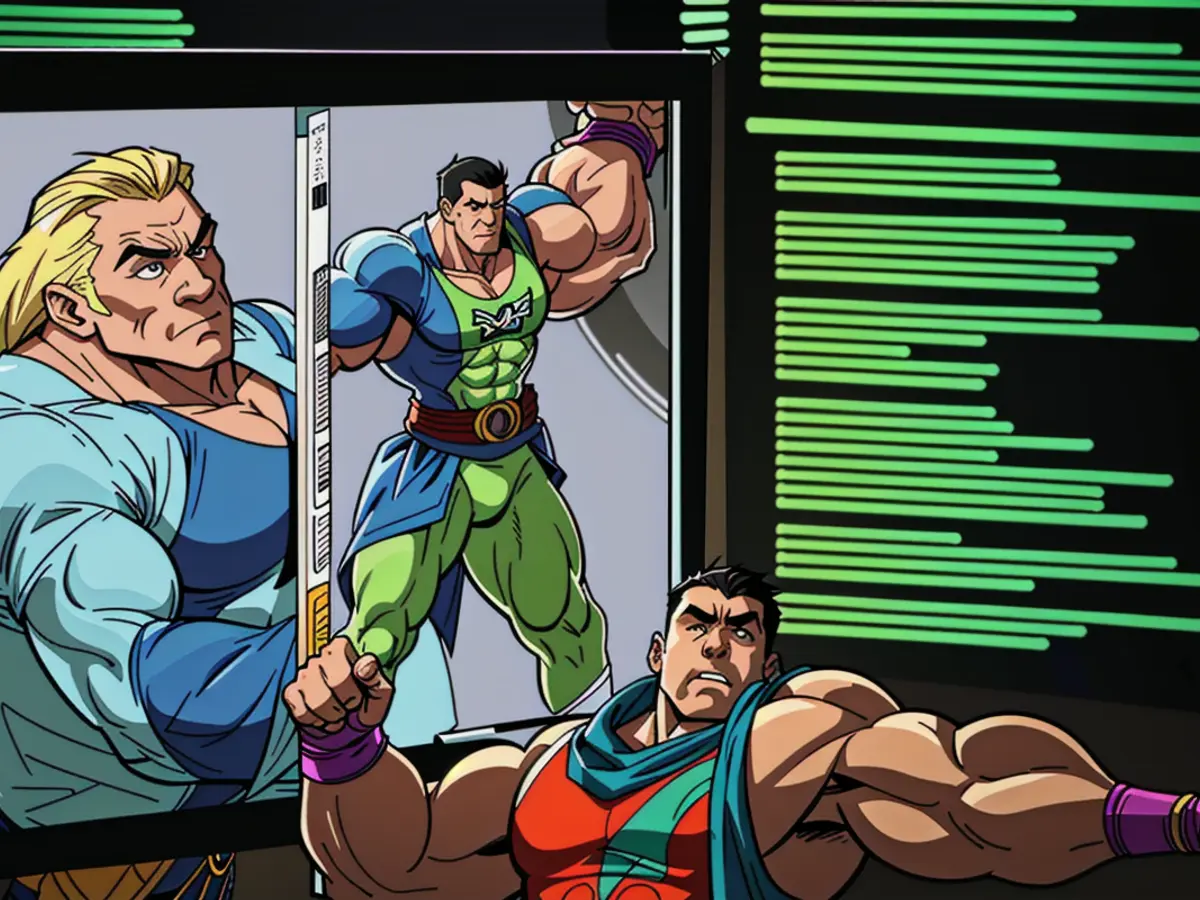
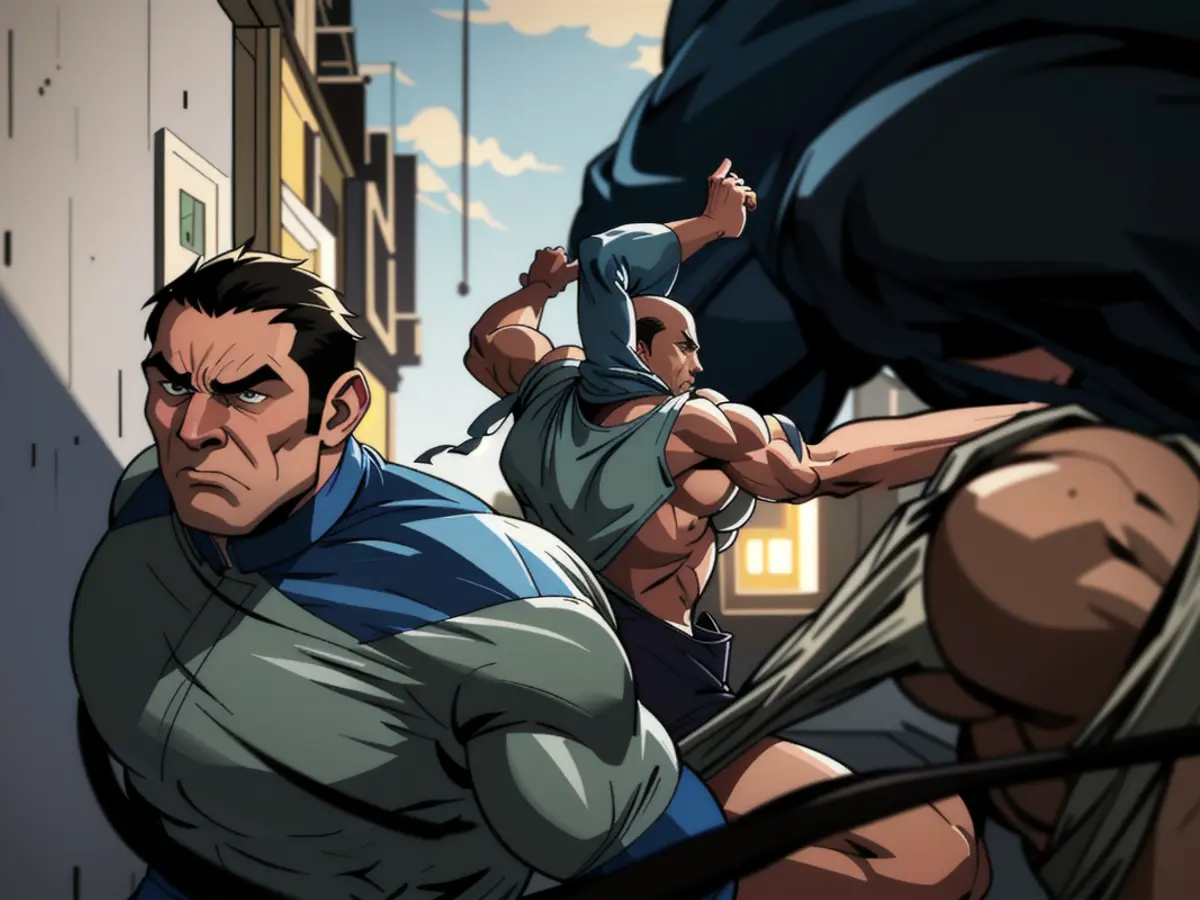
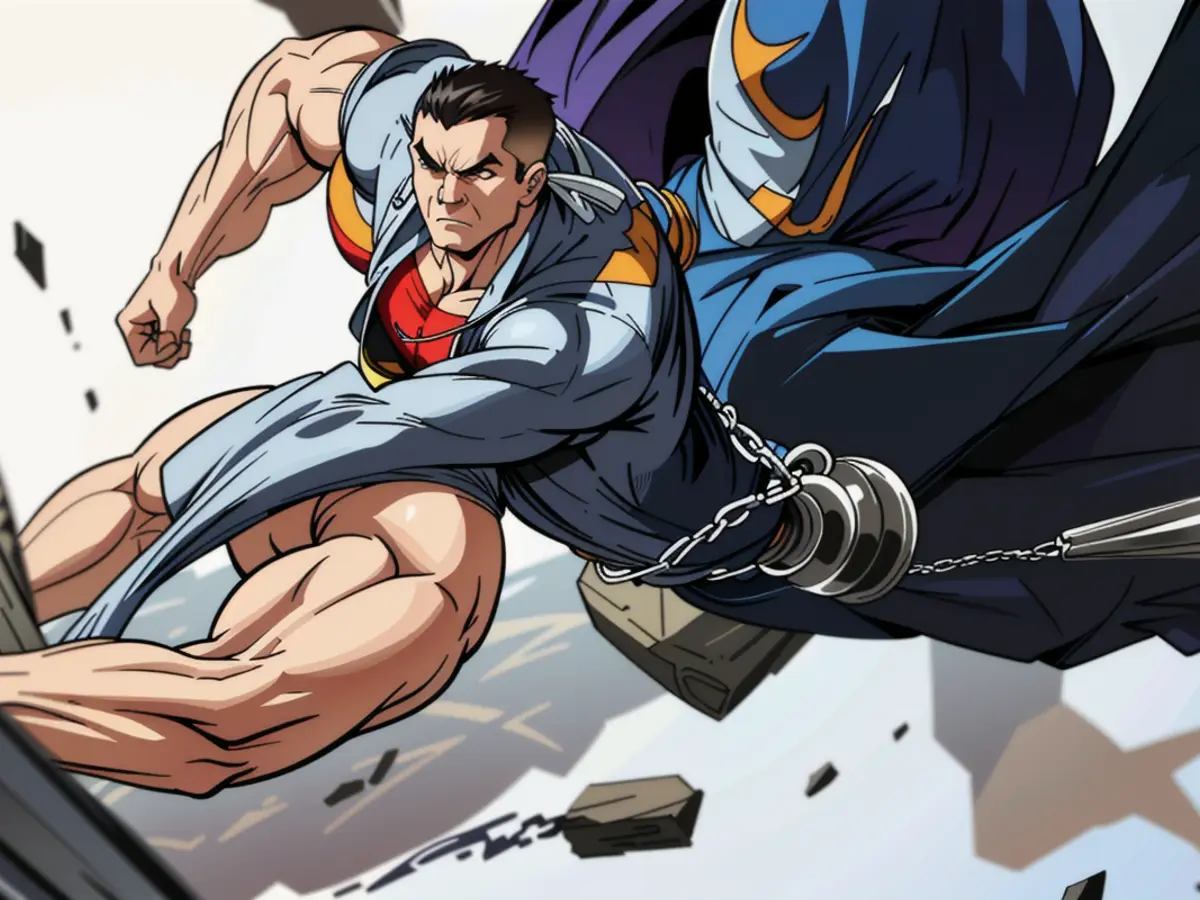